Building Ecologically: as if it were alternative
Mareiner: The construction industry has an enormous appetite: “It devours almost a third of our resources and produces around 40% of our annual waste,” calculates university professor Andrea Rieger-Jandl from the Department of Building History and Building Research at the Vienna University of Technology. As if that wasn’t enough, the production of cement and concrete, aluminium and steel as well as glass and bricks requires enormous amounts of energy. And according to Rieger-Jandl, the buildings constructed with these materials are also responsible for 40 % of our total energy consumption – a devastating balance. While the construction industry is only just discovering recycling after a long delay, there is an urgent need for alternative, sustainable building materials that consume fewer resources and less energy.
Toyota’s car-free eco-city
It is already increasingly being used in urban planning: The automotive group Toyota, of all companies, is transforming a factory site in Japan into a car-free “Woven City” for 2,000 residents according to the plans of Danish architect Bjarke Ingels. The renderings show terraced wooden buildings with large window fronts, numerous beds for vertical gardening and miniature forests on the roofs. If the housing estate model proves successful, it will be built in series.
In view of the busy research and development, it is clear that numerous new sustainable building materials will come onto the market in the coming years and decades. However, there is no need to wait to build ecologically: the alternatives already exist. And have been for thousands of years, so it actually seems wrong to describe concrete and the like as “conventional” building materials.
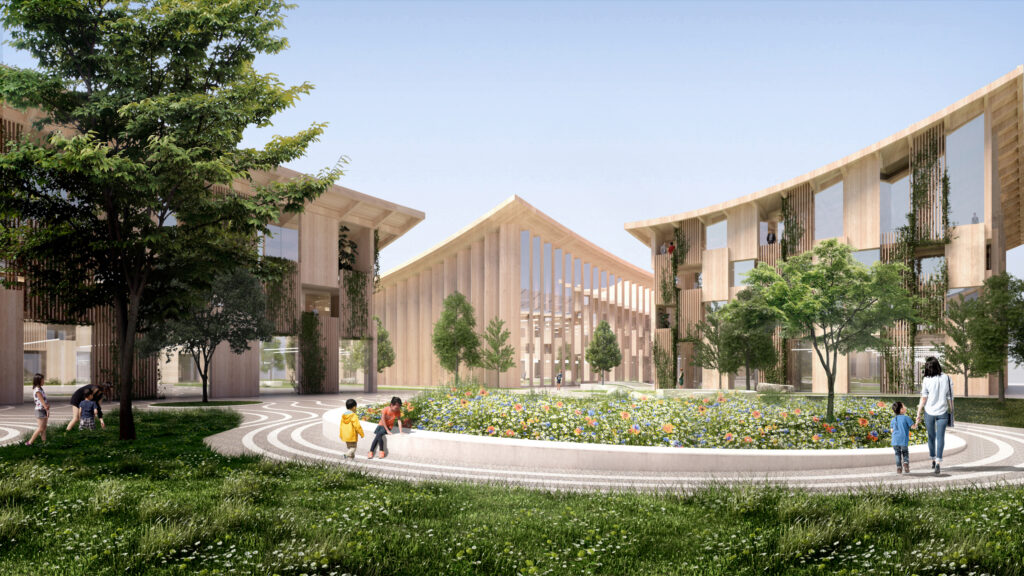
Green true costs
After all, mankind’s building conventions up until the 20th century were for the most part highly ecologically correct. Not least because the building materials used were economical, generally renewable and locally available: the universal building material wood, the almost equally universal clay; then straw as a building and insulating material. Furthermore, hemp, flax and sheep’s wool as insulating materials, reed as a roof covering and – somewhat more modern – wax paper as an alternative to plastic vapour barriers. You can dispense with vapour barriers altogether if you use correctly laid roof tiles – even if their production is energy-intensive.
When weighed against concrete and the like, the pendulum is tipping in favour of bio-building materials overall: the disadvantage of slightly poorer insulation performance is offset by their overall better energy balance and their CO2 storage capacity. As well as their ability to regulate the indoor climate and make it cosy by being largely free of pollutants. Added to this is its ability to retain its insulating properties even when damp.
The biggest drawback is of a financial nature: fully organic construction is five to ten per cent more expensive than conventional construction. This can – and must – change through the greening of housing subsidies and ecological cost transparency in the price of building materials: If the carbon tax that has already been discussed is introduced, concrete will quickly look pretty old compared to wood.
However, eco-construction is not yet possible without concrete, as there is still no green material option for foundations. Glass, which is energy-intensive to produce, will not be replaced so quickly either.
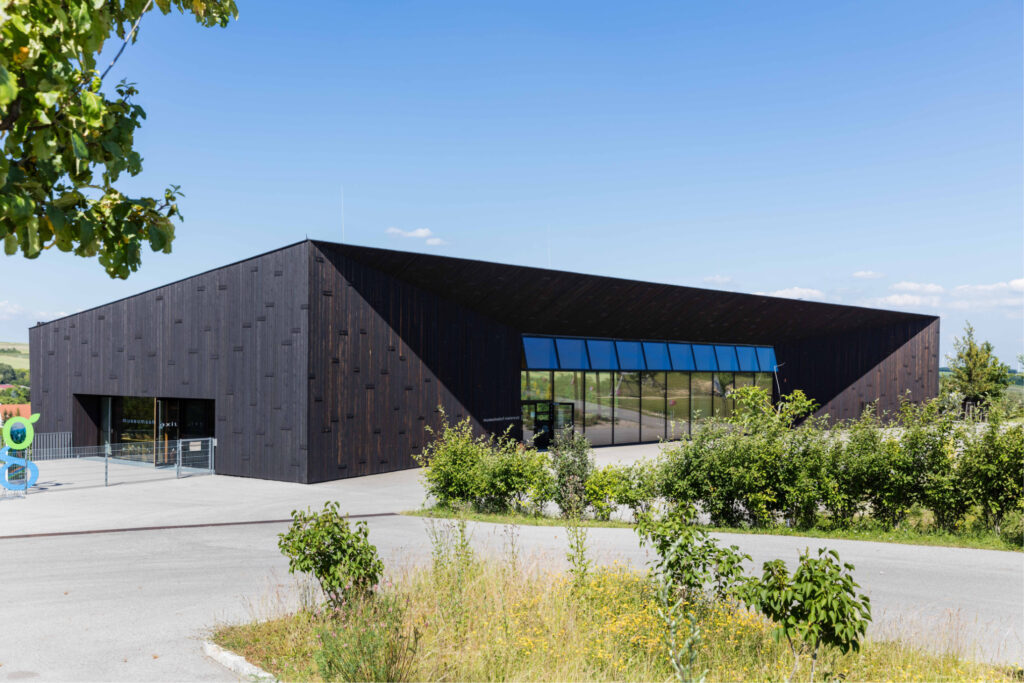
The insulation-free Thoma
The irreplaceability of wood, which epitomises sustainability and versatility, is beyond dispute. Perhaps only that it is also a good insulating material in the form of wood wool and makes a high-quality roof covering when processed into shingles. As Erwin Thoma’s buildings in Goldegg show, you can even do without insulating materials altogether in timber construction as long as you know how to combine the correctly felled wood in various processing forms to create multi-layered wall constructions.
The cheaper alternative to this are timber wall constructions with an insulating core of straw bales; the walls can then be clad with wooden panels or plastered. For example with clay, which will be discussed later.
Houses made of straw, paulownia and reeds
But straw bales are good for more than just insulation: “Straw is also a wall-building material,” says German architect Tilman Schäberle, who, together with his partner Susanne Körner, who is also an architect by trade, built their home in Bad König, Hesse, from a wooden supporting structure and 750 bales of straw at a unit price of 1 euro – it would be hard to find a cheaper building material. The climate was spared in a similar way to the building account: straw is an agricultural by-product and only requires a little tractor and labour power to produce. And the fire risk? As with wood in single-family house construction, it is no higher than that of so-called conventional building materials.
The experimental “Workbox”, which was completed last year as the result of an EU-funded research project by the University of Bonn, Alanus University and Bonn-Rhein-Sieg University of Applied Sciences in Meckenheim, caused a similar stir to Schäberle and Körner’s construction. The bachelor’s thesis by Julian Weber and Raphael Reichert, which has become a reality, has a floor area of just over 20 square metres. All the wood for the construction, floors, panelling and interior fittings was donated by the rapidly growing Paulownia bluebell tree. The thermal insulation of the house prototype, like the insulating plaster and the wall panelling, is made from giant chinese reed, which is characterised by turbo growth and great frugality.
Fast hemp, proven clay
While paulownia and giant china reed are still somewhat exotic building materials in our latitudes, hemp, man’s oldest cultivated plant, is beginning to gain ground again in our everyday lives. In the construction industry, hemp is a first-class insulating material which, in addition to its good building biology properties (air humidity regulation!), also has major ecological plus points: Hemp binds more CO2 during cultivation than its harvest and processing release, improves soil quality with its 1.5 m long roots and grows up to 4 cm a day – without soil fertiliser! – fast enough to keep all weeds in check without chemicals, purely by shading.
A renaissance like that of hemp, which is already being processed into green insulating material on a large scale, is yet to come for clay. Interest in clay plaster is growing again, as it ensures a balanced humidity level of around 50 % indoors – and therefore a healthy indoor climate. “Especially in combination with lightweight timber constructions, the storage capacity of clay is of outstanding importance in terms of building physics,” says Andrea Rieger-Jandl from TU Vienna, “and clay also has proven strengths from a structural point of view, because as built examples show, a combination of wood, straw and clay can also be used in multi-storey residential buildings without any problems.”
A building technique in which the Vorarlberg-born architect Andi Breuss has specialised in recent years. His colleague Hubert Feiglstorfer, on the other hand, is involved in the clay construction working group at the University of Natural Resources and Applied Life Sciences in Vienna, which specialises in this construction method that is steeped in history, particularly in eastern Austria. The aim is not only to preserve the numerous historical earthen buildings as part of Austria’s cultural heritage, for example in the Weinviertel region, but also to initiate new earth building projects – for the benefit of the climate and their future inhabitants.
One of Europe’s leading specialists in modern earth building comes from Austria: Martin Rauch and his Lehm-Ton-Erde office – which is also an earth building contractor – have realised numerous pioneering earth building projects over the past 30 years. His team’s portfolio includes residential buildings as well as public, religious and commercial buildings. Rauch’s earth building credits include the Swiss Ricola AG herbal centre, the Alnatura Campus in Darmstadt, the chancel in Worms Cathedral, the Kardinal Schwarzenberg House in Salzburg and large climate-regulating wall surfaces in Feldkirch Hospital and the Alpbach Congress Centre.
Rationalising clay construction
To realise this, Rauch has developed a mechanical clay tamping process that was previously used directly on the construction site with the help of a rolling machine line. In order to take earth building out of the artisanal corner, the earth building specialist has built a large production hall in his Vorarlberg hometown of Schlins – made of earth, just like his own house, of course. Rauch and his colleagues are now using it to produce rammed earth elements that are intended to help rationalise earth building. One of the first locations for this is the office block that Lehm-Ton-Erde is currently building for itself.
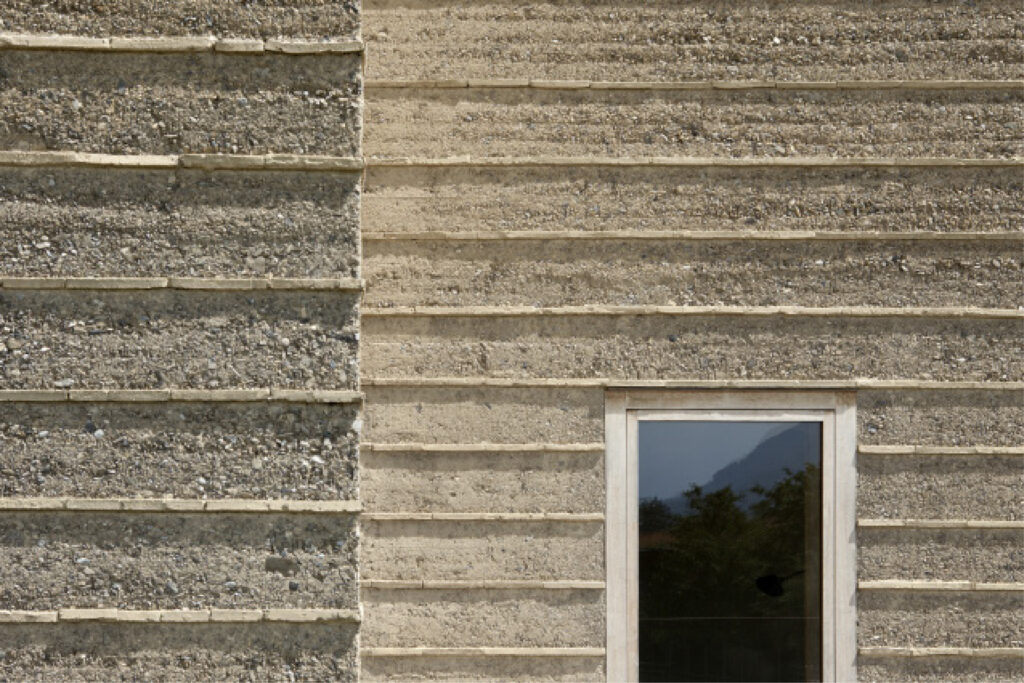
- Clay applications in new buildings and renovation plus contacts to experts gathered at netzwerklehm.at
- The University of Natural Resources and Applied Life Sciences’ clay construction working group is online at lehmbau.boku.ac.at
- Everything to do with building with straw bales can be found at baubiologie.at – the website of the ASBN – Austrian Straw Bale Network